The Challenge
This French manufacturer produces and distributes 20,000 children’s seats for cars every day.
- The mechanical conveying system is inefficient. It requires non-productive manual handling for the plastic trim and often needs to be shut down to be cleaned.
- With 2,500 seats running through every conveying belt in a day, every stop of the machines is quite costly.
- There is an increased risk of accidents when human labor removes the plastic trim manually and especially when they have to remove plastic laying under the conveying belts.
- The mechanical solution produces dust and not only becomes a hazard to the employee’s health but also requires more maintenance in the production facility.
- The process with the mechanical conveying belt and human task of bringing the waste to the container meant a reduced recovery for recycling with the risk of contamination.
- The production facility is less presentable to new customers.
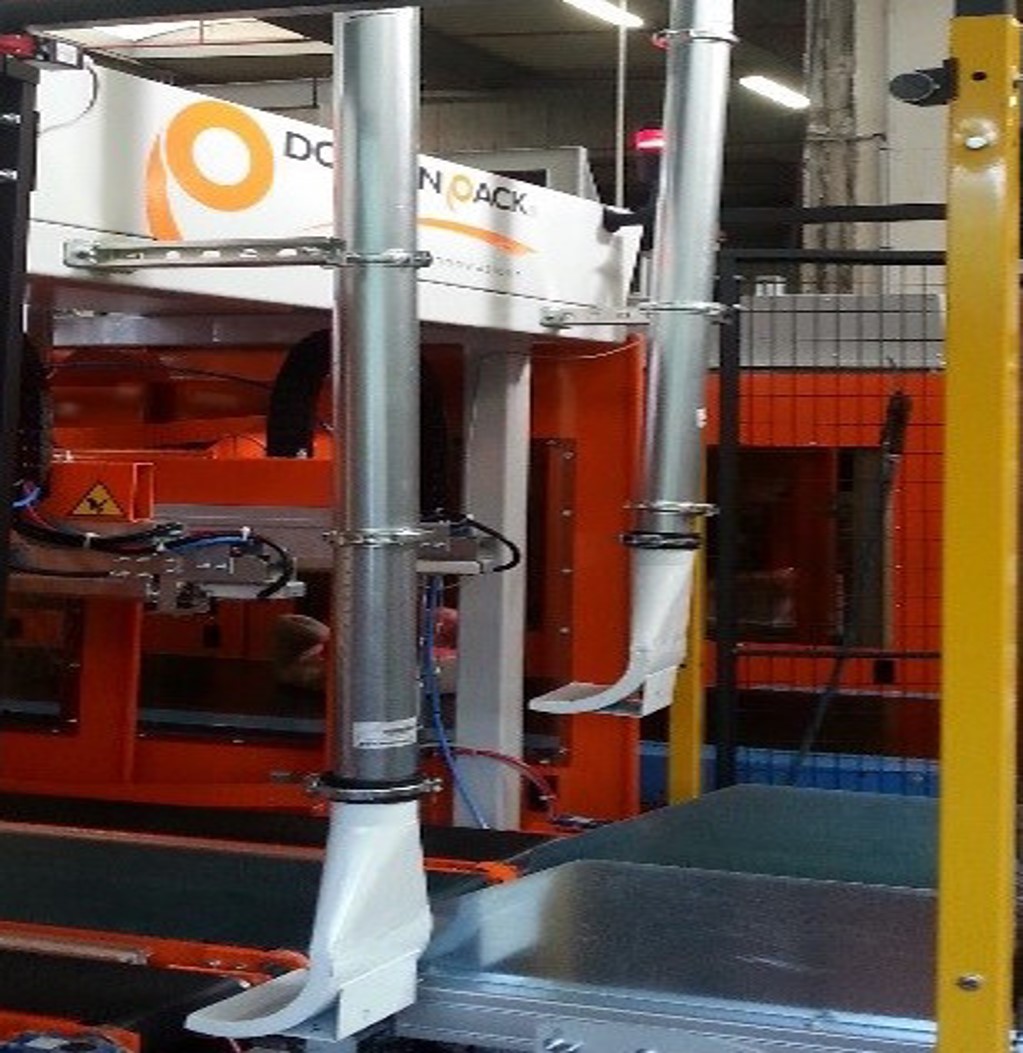
The Solution
The Kongskilde solution consists of a MultiAir 1075T blower and the inline Venturi system ITF 160 which together with the FK 80, FK 120 and OK160 piping secures efficient handling of the plastic trim from all eight conveying lines.
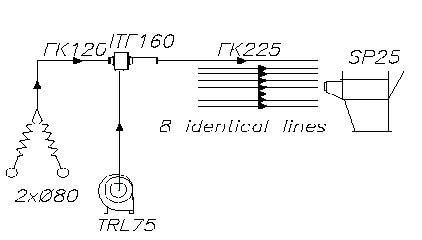
The Advantages and Benefits
- The pneumatic solution is safe since no one has to remove trim waste around and under the machinery.
- The Kongskilde solution increases productivity as the customer doesn’t have to use labor to remove the plastic trim and transport it to the container outside the factory.
- Continuously running all eight conveying belts contributes to an even more efficient production.
- Less need for maintenance of the pneumatic conveying solution and even less need for cleaning the factory without the dust issues gives a net cost saving.
- More space around the machines improves safety and productivity contributing to better working conditions.
- The removal of dust improves working conditions and makes the production lines more presentable.
- Better recovery for recycling and elimination of external contamination in the compactor due to the closed system.
The Facts
- Material: PE packaging film
- Thickness: 15 microns
- Waste size max: 1,000 mm x 150 mm
- Speed of production: 7 rounds/min or 400 rounds/hour
- Number of machines: 8 with two pick-up points to each
- Max. Transport distance: 60 m
- Max lift: 6 m
- Number of elbows: Five