The Challenge
A US-based factory specializing in automotive components such as door panels, bumpers, HVAC ducts, and fluid systems, needed to increase the amount of Post-Industrial Recycled (PIR) resin in their finished products without compromising quality and creating production delays.
- The company also wanted to correct serious housekeeping issues caused by the existing granulator evacuation system.
- Dusty regrind limited PIR content in finished products to 30%. Even at this low recycled-to-virgin ratio, vacuum pump filters and screens became blocked causing frequent production delays.
- The new solution had to reduce the amount of dust in their regrind, reduce fugitive dust created by the evacuation blower and have a short payback period.
The Facts
- Material: HDPE Regrind
- Bulk density: 35 lbs./ft³
- Particle size: 3/8”
- Rate: ~650 lbs./hr. (295 gram/hr)
- Number of machines: 30+ individual machine side grinders that all require AirWash units.
The Solution
- The Kongskilde solution consists of the AirWash 50 and K-200 dust collector. Material is evacuated from the granulator directly into the Airwash using a Kongskilde OK pipe system.
- The AirWash is a sealed, negative pressure conveying and cleaning process. Dust is drawn in and never blown out onto the production floor
- It is important to note that the material does not go through the fan. This feature prevents blower rotor and housing failure, along with reducing dust and granule degradation.
- The AirWash’s two-stage cleaning system removes dust from the granulate and the output is ready to be blended with virgin resin and reintroduced directly into the molding machine.
- The AirWash 50 is equipped with a 5 HP fan motor and a 0.75 HP motor for the rotary airlock.
- The conveying air is filtered through the K-200 bag house. Dust is collected in sealed steel cans with sight glass. This simplifies dust disposal compared to traditional hanging dust socks, which are messy to empty.
The Advantages and Benefits
- After the installation of the Kongskilde system, PIR content in select products went from 30% to 80%, leading to significant financial savings.
- Eliminating dust from the regrind enabled the inclusion of more PIR in each product without compromising quality, while also reducing the need for cleaning screens and vacuum loader filters.
- The housekeeping workload was dramatically reduced, while the respiratory health and safety of production floor workers immediately improved with the elimination of dust particles.
- The AirWash allowed greater use of recycled material without compromising quality and had the added benefit of reducing dust on overhead structures, floors and production equipment. The company saw an immediate financial gain through lower per-piece costs.
- Additionally, there were lower insurance premiums due to improved worker safety and reduced risk of dust fires.
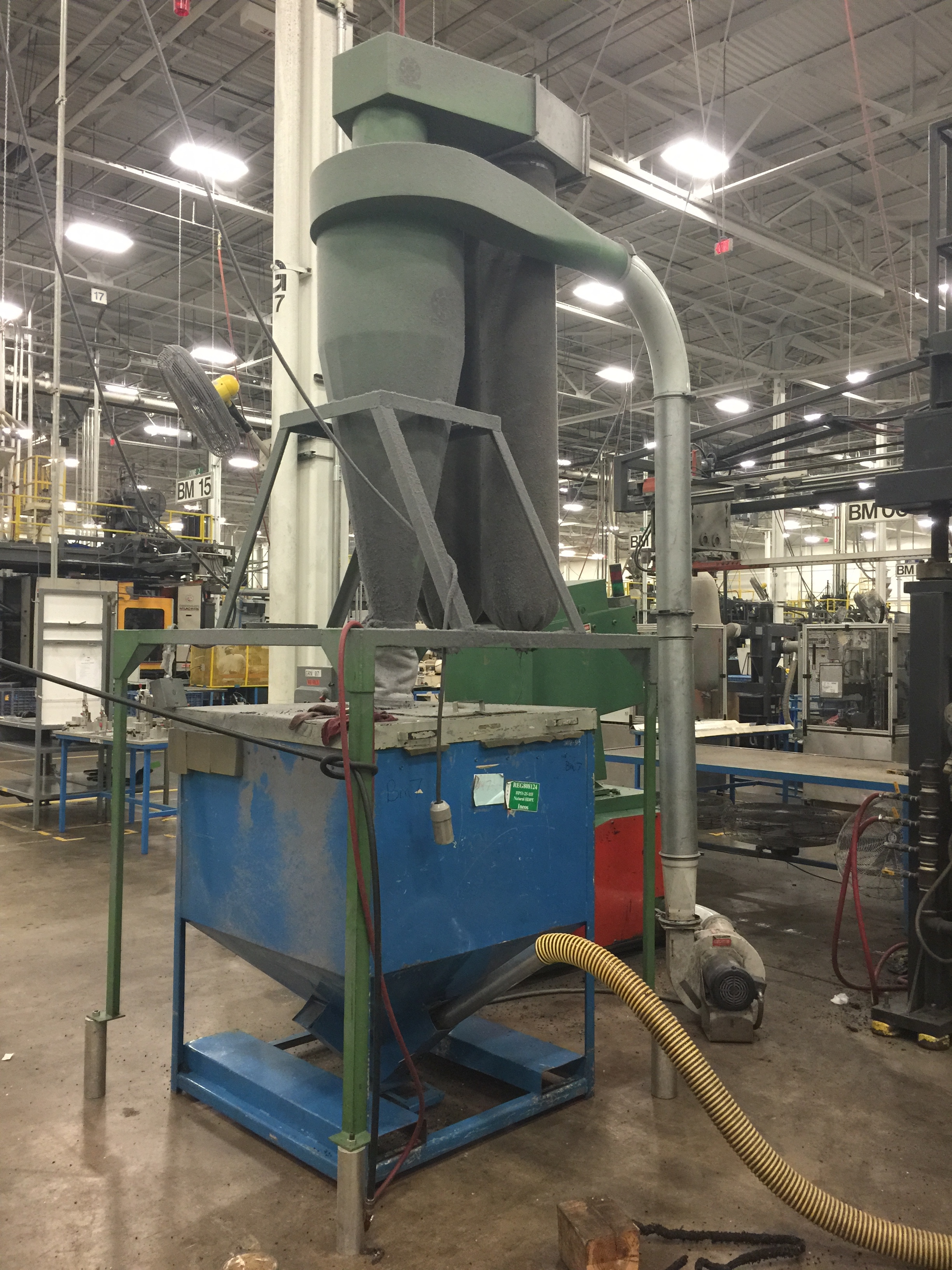
Before the Kongskilde system was installed, the granulator was evacuated with a “material-through blower” and open bottom cyclone. This process damaged the regrind and created additional dust. Only a minimal amount of fines ended up in the filter socks.
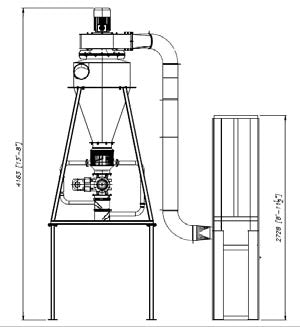

After the Kongskilde system was installed PIR content in select products went from 30% to 80%, leading to significant financial savings.
Ready to see more?
See how Kongskilde’s air-based solutions solved problems in different industries.