The Challenge
This Belgian manufacturer produces high-performance extrusion coated and multilayer products. In this case the company coats “throw-away” overalls.
The customer wished to replace the old cutter, which had to fit into the existing production line with the existing blower and pipes diameters and deliver at least the same capacity as before
The Solution
There were no details on specs from the current blower or pipe diameters. Kongskilde had to run some tests in the Technology Centre to make sure the cutter would fit the system.
It turned out that the Kongskilde MultiCutter MC 3000 could handle the job. But to have the lowest backpressure, the solution needed to be the MC 5000.
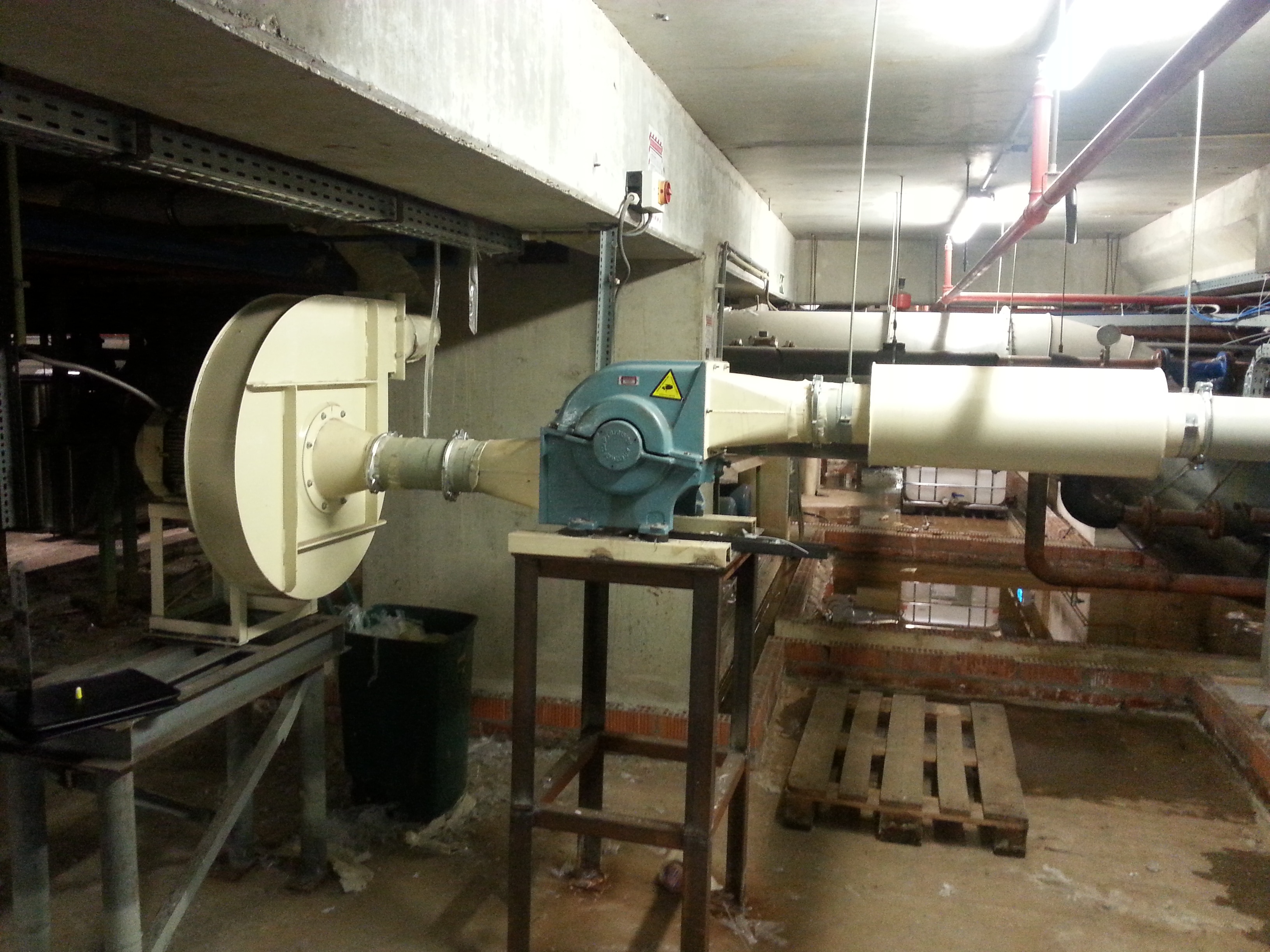
The Advantages
- The flexibility of the Kongskilde conveying solutions and in this particular case with a MultiCutter makes it scalable and able to fit into both older and newer systems.
- The modularity proves to be a cost-effective way to upgrade systems by only replacing, e.g., the MultiCutter.
- The Kongskilde elements can be set up very quickly, and with access to the Kopngskilde Technology Centre, the customer can be sure to receive the best future-proof solution here and now.
The Facts
- The Kongskilde Multicutter MC5000 was installed.
- It was fitted with the existing multi blower and piping system to handle the current trim suction.
- The test lasted for six months, and it turns out that the MC5000 is the perfect match for the existing system, and it is now a part of the production line.