The Challenge
- A factory located in Poland is a well-known tea producer for the domestic and international markets.
- The client has two machines with the ability to extract bags, and six machines where the cutting and handling of trimmings take place.
- The small diameters of the exhaust pipes on the machines are due to the need to overcome high pressure in the system.
- Before the system was in place, it was necessary to extract trimmings through local exhausts, causing a need for additional employees.
- Local exhausts were causing numerous downtimes and messes during the production process, and were taking up room in the production hall.
- The company needed a solution for the extraction of trimmings in order to ensure cleanliness in the production area and increase productivity while keeping downtime, and the number of personnel members operating production equipment, to a minimum.
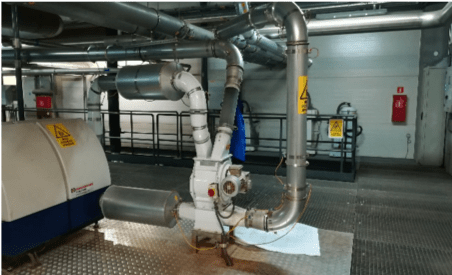
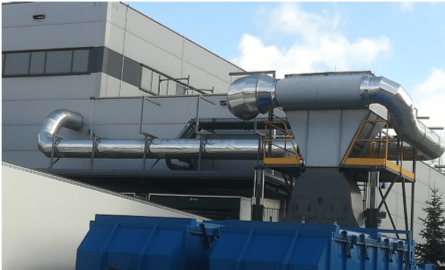
The Facts
Machine nos 1-2
- Material: Paper (tissue), plastic film
- Dimensions: 120 x 120 mm
- Material weight: 21 g/m2
- Quantity: 150/min.
Machine nos 3-8
- Material: Paper – continuous cutting and extraction
- Trim width: 12 mm
- Material weight: 21 g/m2
- Speed: 17.5 m/min.
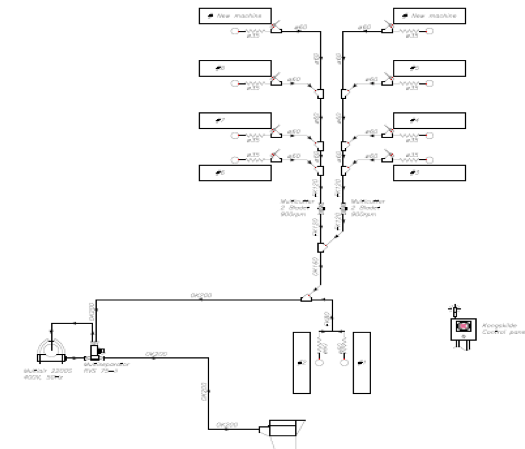
The Solution
- The system includes dust suction points with pressure sensors.
- The installation was divided into three separate lines where the lift force is generated by BTK fans.
- All dust is separated from the transported air by the bag filter (KNFK) and discharged to a large bag with a dust-level indicator.
- All of this is controlled by an intuitive control device.
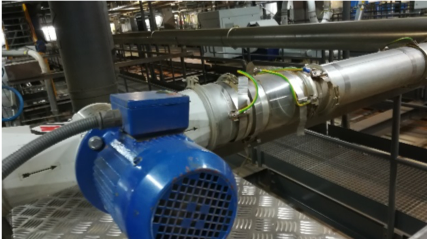
The Advantages and Benefits
- Kongskilde’s solution collects inline waste – there is no longer a need to stop production for cleaning.
- The risk of accidents has been significantly reduced.
- Equipment failures are minimised.
- Downtime of control equipment has been reduced.
- The return of air from the filter has lowered heating costs.
- Dust collection significantly facilitates logistics, and allows it to be further processed or resold.