The Challenge
This US-based company, a leader in the American plastic bag industry, needed a flexible and reliable conveying system to transport PP and PE pellets from rail cars.
- The setup included space for up to five rail cars, each with four ports for pellet extraction, which then needed to be blown into any of ten 31-meter high silos within a stringent timeframe.
- The system had to ensure zero contamination, including moisture and foreign materials, as any contamination could lead to significant economic losses.
- Additionally, the solution had to be more cost-effective in terms of total ownership compared to their previous PD pump system.
The Facts
- Material: PP and PE Pellets
- Dimensions: pellets max Ø 3mm, grid max Ø 1mm
- Requested solution providing a flow of 15-20 metric tons of pellets per hour to the 31 meter high silos
- Bulk density: approx. 520 kg/m3
- Conveying distance: H: max 31 m. V: max 28 m
The Solution
The Kongskilde conveying system provided a reliable, contamination-free solution that met the operational and economic needs of a major US plastic bag producer. The system’s modularity and cost-effectiveness ensure it remains a sustainable choice for future expansions and ongoing efficient operations.
The solution involved using modular standard elements to create a conveying system that efficiently transported the pellets from the rail cars into the silos without contamination. Key components included:
- Two Kongskilde TRL 600 Blowers: These were used to manage the distance and maintain low air temperatures, ensuring a high-performance pneumatic solution free from contamination.
- Modular Design: The system’s flexibility and modularity allowed for easy installation and future upgrades, such as adding new pipelines when additional silos are built.
- Cost Efficiency: The Kongskilde system proved to be a cost-effective investment with lower operating and maintenance costs compared to previous systems.
The Advantages and Benefits
Upon implementing the Kongskilde system, the company swiftly reaped numerous advantages and benefits.
- High Flexibility and Modularity: Facilitates easy installation and meets specific requirements. Future expansions, like adding new silos, are cost-effective with simple pipeline installations.
- Contamination-Free Solution: The high-performance system ensures safe operation without risking pellet contamination.
- Minimized Heat Build-Up: Using two blowers reduces heat build-up, preventing the formation of “streamers” in the pipeline.
- Low Maintenance Costs: The pneumatic solution’s design reduces the need for frequent maintenance, contributing to lower operational costs.
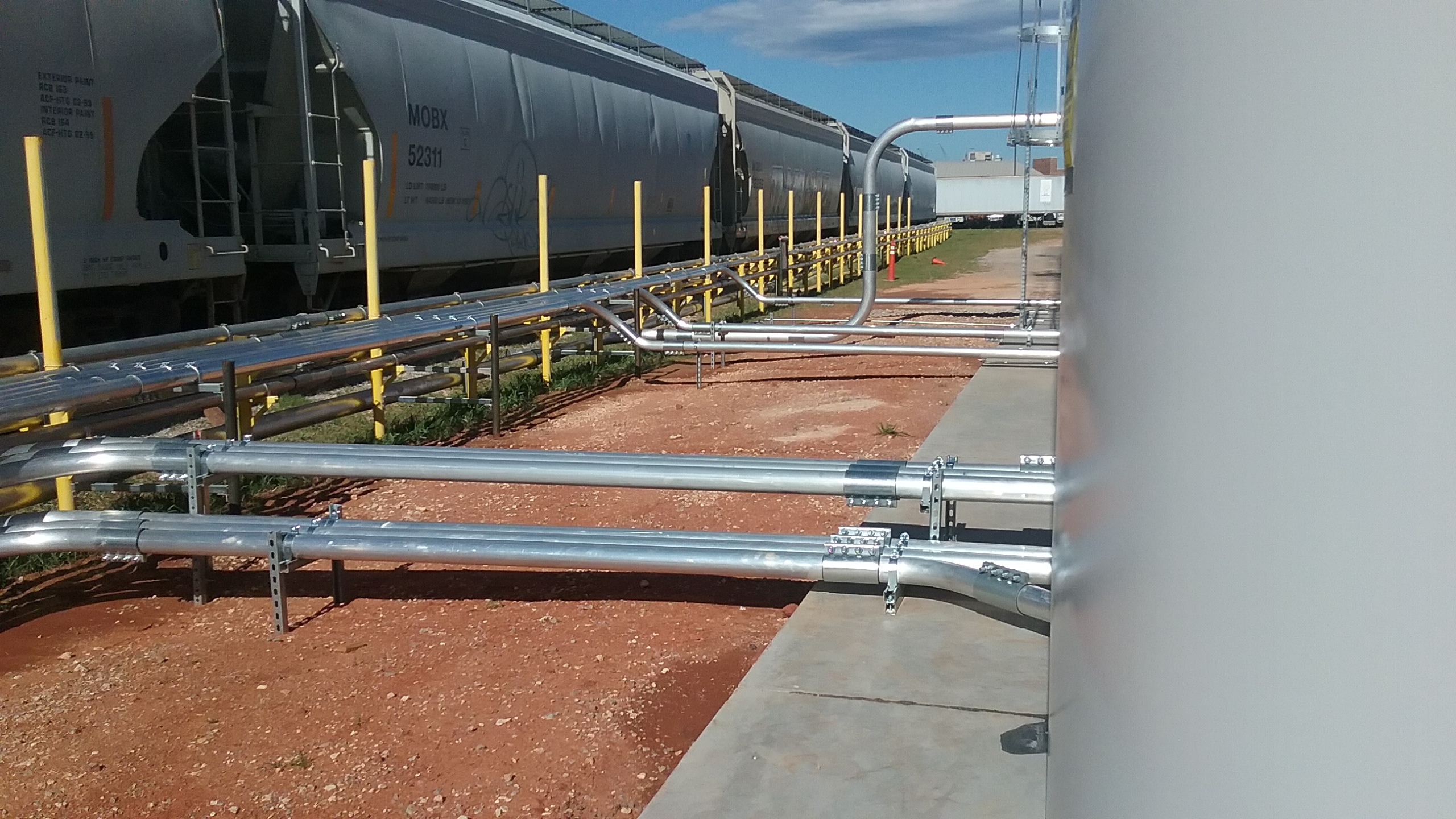
For future silo installations, upgrading the system is more cost-effective. Kongskilde simply installs a new pipeline, making the process efficient and economical.
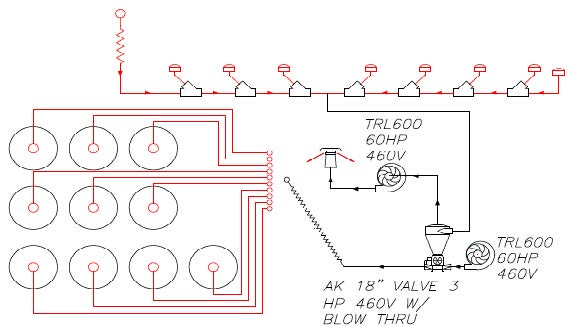

Before the Kongskilde system was installed the company used a PD pump system, which posed higher risks of cross-contamination, consumed more energy, and required frequent maintenance due to wear and tear.
Download the full case study:
Ready to see more?
See how Kongskilde’s air-based solutions solved problems in different industries.