The Challenge
A world-famous company located in France produces and distributes liquor. The bottles for the liquor come in pallets wrapped in plastic in three lines
- The company needed a solution to eliminate costly human resources used to transport the unmanageable plastic wrap from the three lines into the compactor outside the production facility.
- The solution should contribute to improving the working environment by reducing the dust coming from plastic wrapping. At the same time, the solution should reduce the cost of maintenance in the production facility
- Since noise is always an issue at this kind of production line, the solution has to reduce the noise level to contribute to improving the working environment for the employees
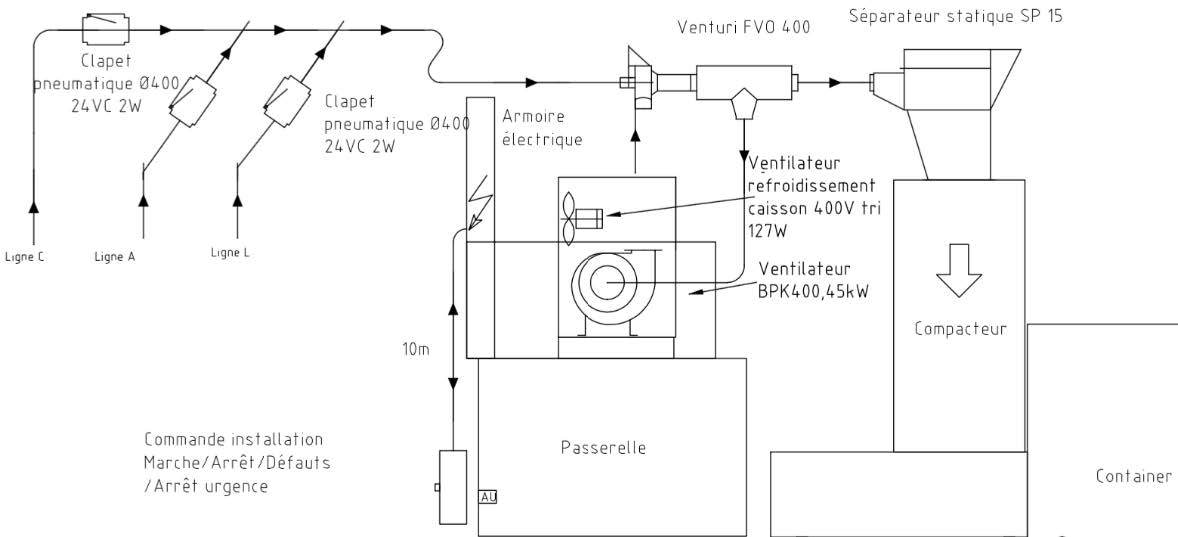
The Solution
- The pneumatic conveying removes the plastic wrap in a split second from the three pick-up points. By using an automatic gate, it is possible to regulate the time of opening of each hopper according to the speed of the lines. There is plastic wrap to be transported every 30 sec.
- The Kongskilde solution consists of a blower BTK 400 45Kw which blows air into the Venturi FVO 400 to create negative pressure in the diameter 400mm.
- The customer deposits the plastic cover into a specific pick-up point then it is automatically carried into the static separator SP 15 placed over the compactor inlet.
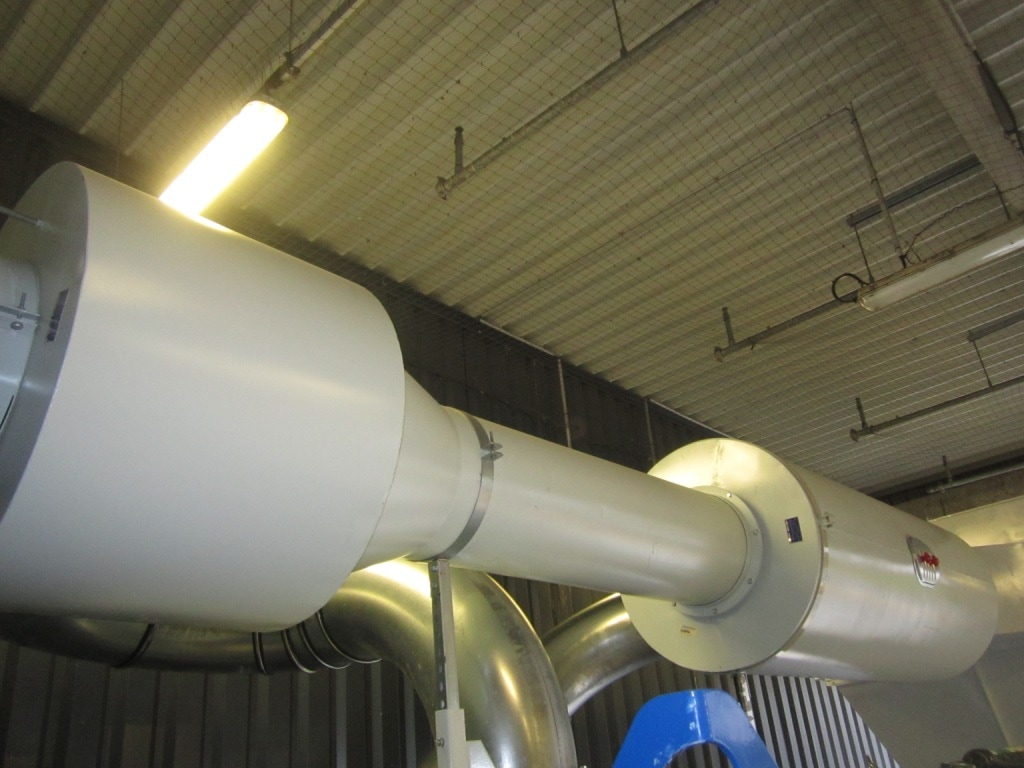
The Advantages and Benefits
- The Kongskilde solution increases efficiency and saves money as the customer doesn’t have to use the workforce to transport the plastic wrapping to the outside container
- This eliminates the risk of accidents with forklifts inside the production room and reduces labor-cost related to manual waste handling inside the factory by 30%
- No chance of contamination of the plastics to be recycled
- More space around the machines improves productivity
- The factory environment is cleaner as dust from the plastic films is now eliminated creating a healthier working environment. At the same time, the maintenance of the production facility is minimized considerably
- The noise reduction in the system also contributes to a better working environment for the employees
- ROI for this system is 12 months
The Facts
- Material: Plastic film in two or three thickness
- Requested solution: customer need to convey the plastic wrapping from three lines to an outside compactor
- Suction points: 3
- Size: 1200 mm x 4300 mm
- Bulk density: 4 kg per film
- Conveying distance: H: max 80 m. V: max 5 m