Oparte na danych monitorowanie energii i optymalizacja procesów w Przemyśle
Kongskilde Industries uczestniczy w projekcie mającym na celu zmniejszenie emisji CO₂ w wyniku elektryfikacji przemysłu wytwórczego i przetwórczego. Można tego dokonać poprzez cyfryzację wszystkich ogniw w łańcuchach wartości firmy, zapewniając dane potrzebne do podejmowania decyzji opartych na dowodach w planowaniu produkcji. Oprócz Kongskilde Industries, uczestnikami projektu jest największa grupa odlewnicza w Europie Północnej Vald. Birn, konsultant IT Fellowmind, duński uniwersytet SDU oraz dostawca oprogramowania Inuatek A/S. Projekt jest prowadzony przez Energy Cluster Denmark.
Poniżej znajdują się fragmenty artykułu opublikowanego w duńskim czasopiśmie branżowym Maskinbladet.
„Wkraczamy w Przemysł 4.0, gdzie dane z produkcji i procesów mają kluczowe znaczenie, dlatego w przyszłości musimy być w stanie zaoferować naszym klientom oparte na danych i inteligentne rozwiązania do optymalizacji ich produkcji i procesów, w tym zużycia energii”.
Steen Hansen, kierownik ds. badań i rozwoju, Kongskilde Industries A/S
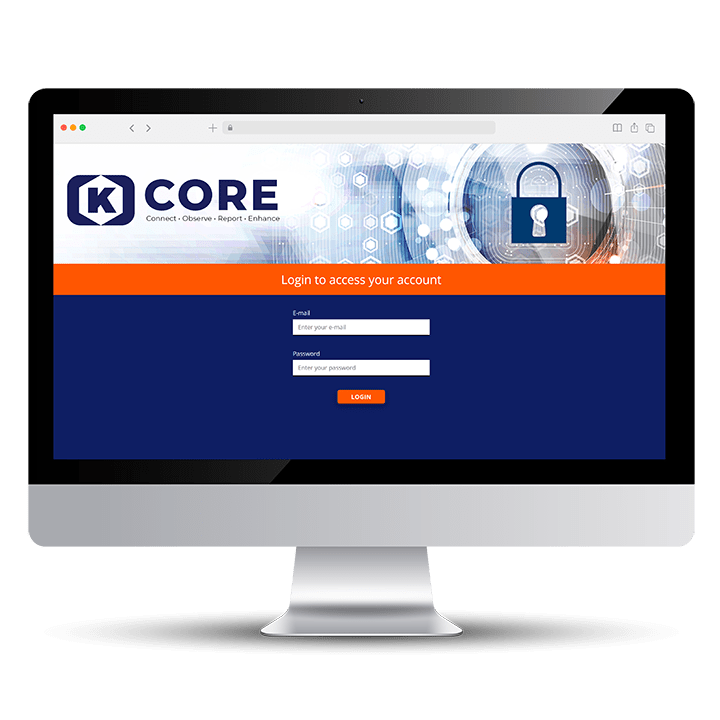
Jesienią 2022 roku Kongskilde Industries uruchomiło swoje pierwsze rozwiązanie chmurowe do gromadzenia i analizy danych. Rozwiązanie umożliwia zarówno klientowi, jak i Kongskilde ciągłe monitorowanie produkcji przy użyciu danych zebranych za pomocą czujników z procesów produkcyjnych. „Dla naszych klientów chodzi o zużycie energii, ale także o niezawodność oraz planowanie serwisu i konserwacji. Wymaga to nowych rodzajów systemów monitorowania, a my je rozwijamy” – kontynuuje.
Kongskilde zazwyczaj dostarcza systemy wykorzystujące pneumatykę do wspomagania produkcji, gdzie na przykład odpady lub pył są zasysane lub wydmuchiwane. „Nasze systemy zwykle stanowią niewielką część całkowitego zużycia, ale ważne jest, aby systemy działały stabilnie i optymalnie ze względu na niezawodność, konserwację i zużycie energii” – mówi Steen Hansen.
Model biznesowy jest rozwiązaniem dodatkowym do istniejących systemów Kongskilde. „To od klientów zależy, które komponenty lub procesy chcą monitorować. Mogą to być silniki, wentylatory lub filtry. Na przykład, gdy filtry się zapychają, wpływa to na zużycie energii, niezawodność i żywotność” – mówi Steen Hansen.
Połączenie danych w czasie rzeczywistym i przetwornic częstotliwości będzie również w stanie zoptymalizować zużycie energii, tak aby działała tylko niezbędna dmuchawa. Pozwala to uniknąć stałych ustawień, które czasami powodują niepotrzebne zużycie energii. „Dzięki danym w czasie rzeczywistym możliwe będzie zmniejszenie prędkości dmuchaw bez spadku produkcji. Celem jest dynamiczne dostosowanie dostaw. Optymalnie, procesy przebiegają w pełni automatycznie, unikając ryzyka błędu ludzkiego, który może wpłynąć na proces w niewłaściwy sposób. W pełni zautomatyzowane rozwiązania wymagają jednak odpowiedniej konfiguracji warunków wstępnych. Wszystkie ważne i niezbędne parametry produkcyjne i energetyczne muszą być zintegrowane z rozwiązaniem. Projekt pomoże nam dowiedzieć się więcej na ten temat” – podsumowuje Steen Hansen.
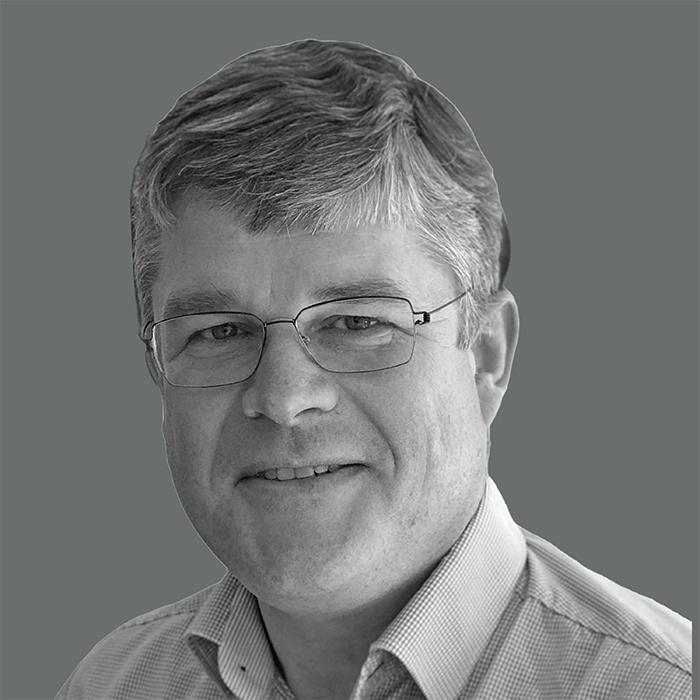