Le défi
- Ce grand producteur français de yaourts souhaitait éliminer les déchets plastiques de cinq lignes de production.
- En même temps, l’entreprise voulait éliminer le travail manuel consistant à retirer régulièrement deux boîtes en plastique par ligne de production de la zone de production vers le conteneur à déchets.
- Le producteur de yaourts souhaitait séparer les étoiles de différentes couleurs (une « étoile » est la partie en plastique coupée au milieu d’un pack de 4 yaourts).
- L’entreprise avait un coût de 9 000 euros par mois pour le transport et la manutention des déchets en vrac non triés vers l’entreprise de recyclage.
Les faits
- Matériau : Polystyrène
- Dimensions : Min. 8,5 x 8,5 mm, Max 20 x 20 mm
- Distance de transport : 30 mètres
La solution
- Le système se compose d’un multi-séparateur Kongskilde, le RVS, qui permet l’élimination par aspiration des déchets des 5 lignes de production de yaourts.
- Il est équipé d’une soufflante BPD 30 kW, conçue pour la manutention des matériaux par les soufflantes. Il est équipé d’un rotor autonettoyant, qui possède des pales incurvées vers l’arrière et une entrée aérodynamique.
Les avantages et les bénéfices
- Plus de 8 tonnes de déchets de production récupérés et revendus aux fournisseurs de matières premières à environ 200 euros la tonne.
- Réduction des coûts de traitement des déchets par l’entreprise de recyclage.
- Les déchets sont désormais transportés directement dans des bigbags, ce qui permet d’économiser 9 000 euros par mois grâce à la réduction des coûts de transport par rapport aux conteneurs entiers.
- Le délai de récupération prévu est inférieur à trois ans.
- Des lignes de transport individuelles à partir de chaque machine de production permettent de séparer les différents déchets/couleurs.
- Élimination des besoins en personnel pour le transport interne des petits conteneurs de la zone de production vers les conteneurs extérieurs.
Téléchargez l’étude de cas complète :
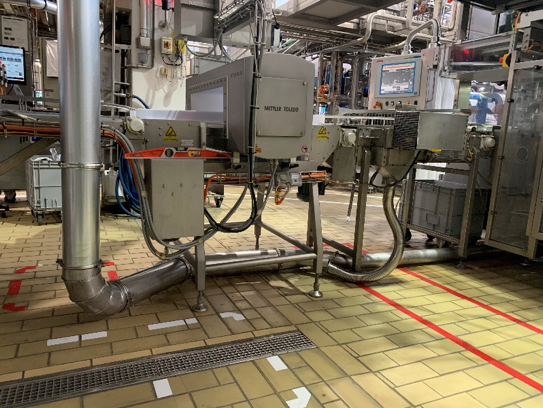
Les lignes de transport individuelles de chaque machine de production permettent de séparer les différents déchets et couleurs.
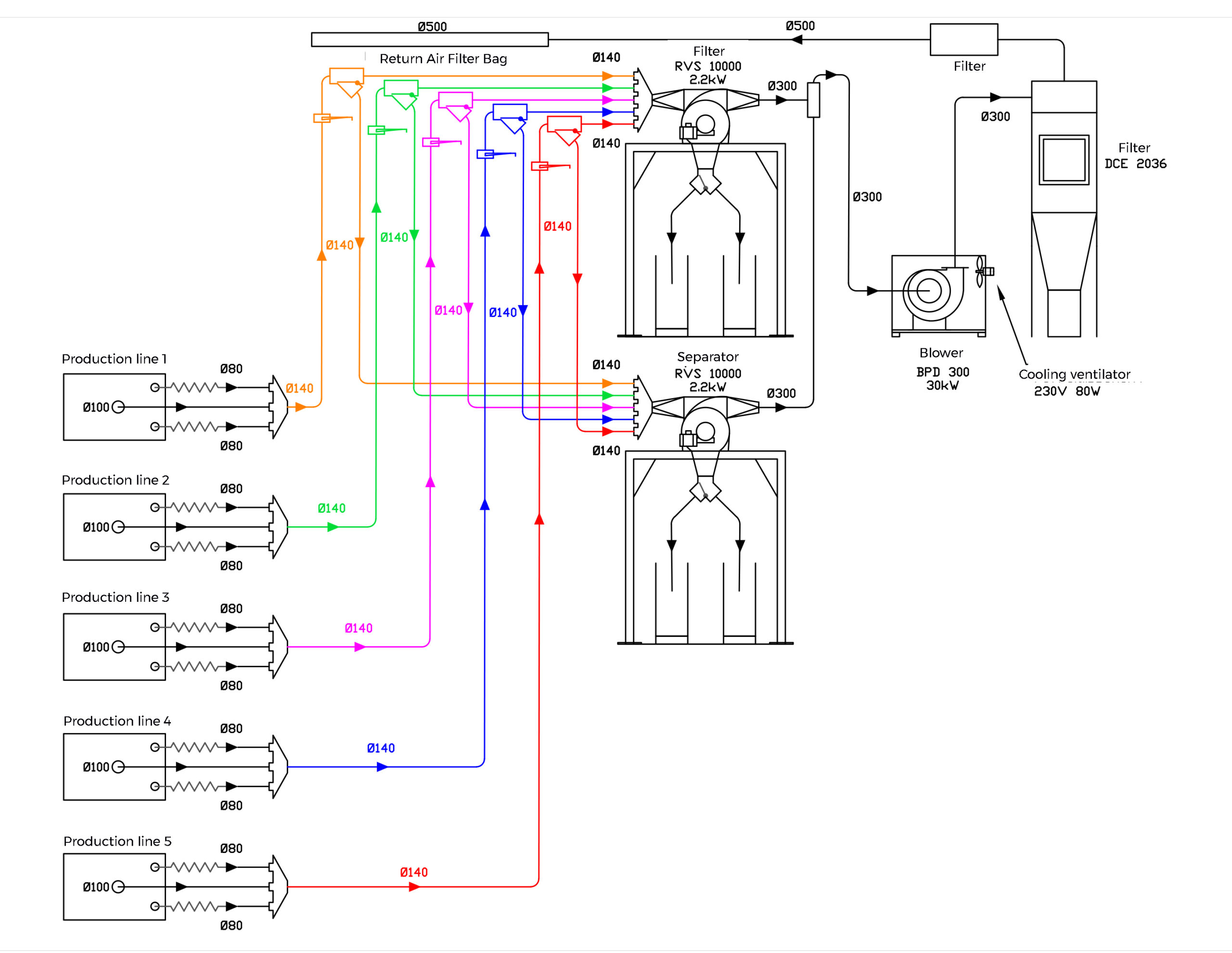
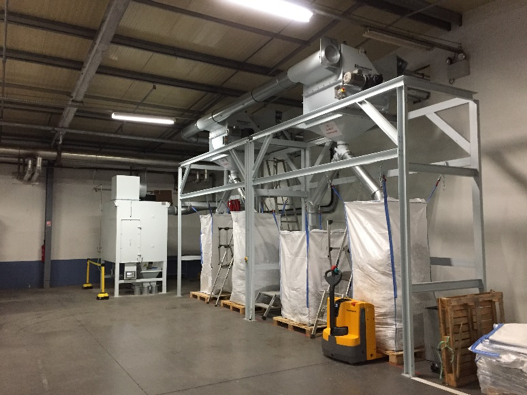
Après l’installation du système Kongskilde, les chutes sont désormais triées dans des bigbags. le système Kongskilde a été installé, les chutes sont désormais triées dans des bigbags, ce qui permet de réaliser d’importantes économies mensuelles.
Vous voulez en savoir plus ?
Découvrez comment les solutions aériennes de Kongskilde ont résolu des problèmes dans différentes industries.