Le défi
- Une multinationale de biens de consommation possède une usine en Europe pour le remplissage et le bouchage de produits en bouteille.
- Deux machines à capsuler appliquent différents types de bouchons pour les bouteilles. Les bouchons sont stockés dans des boîtes au sous-sol, sous le 1er étage où fonctionnent les machines à boucher.
- Avant l’installation du système pneumatique, une palette contenant des boîtes de 2 500 pièces. a été déplacée, palette par palette, entre
les étages par un chariot élévateur et un ascenseur. - L’entreprise avait besoin d’une solution qui éviterait à l’opérateur d’avoir à découper les boîtes et à les soulever pour verser les bouchons dans la machine à capsuler et qui éviterait également l’utilisation d’un chariot élévateur.
- L’entreprise a demandé un système qui éliminerait la logistique du transport des palettes par un cariste, afin de gagner du temps et d’améliorer la sécurité.
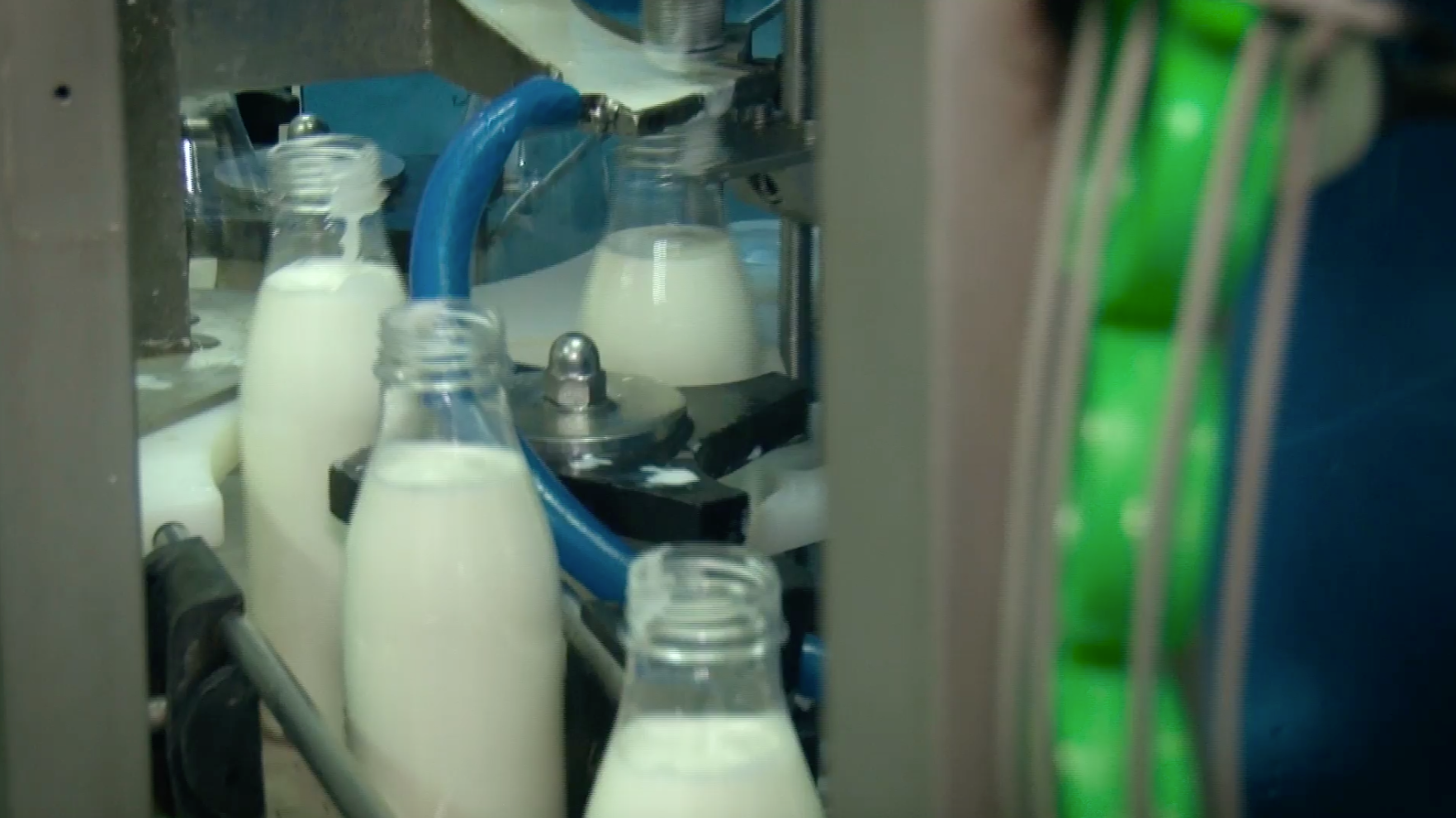
La solution
- 2 pièces. Unités de prise en charge des composants (CPU)
- 2 pièces. Chargeurs à vide de composants (CVL)
- Tuyauterie, jusqu’à 50 mètres
- Souffleur, MultiAir FC 1100
La solution Kongskilde comprend deux unités de prélèvement des composants (CPU), des tuyaux en plastique spécialement sélectionnés avec une surface lisse pour éviter de rayer les surfaces des composants, un ventilateur (MultiAir FC 1100 S), et deux chargeurs sous vide de composants (CVL) pour la livraison par lots dans la production.
Chaque unité centrale vide les conteneurs du sous-sol à raison de 10 000 bouchons par heure. Lorsqu’elle est vidée, l’unité centrale se met en veille, le cariste change le conteneur et appuie sur le bouton de démarrage. L’usine fonctionne 24 heures sur 24 et 7 jours sur 7 en trois équipes.
Les CVL livrent les bouchons au rythme requis de 10 000 pièces. par heure aux machines à capsuler.
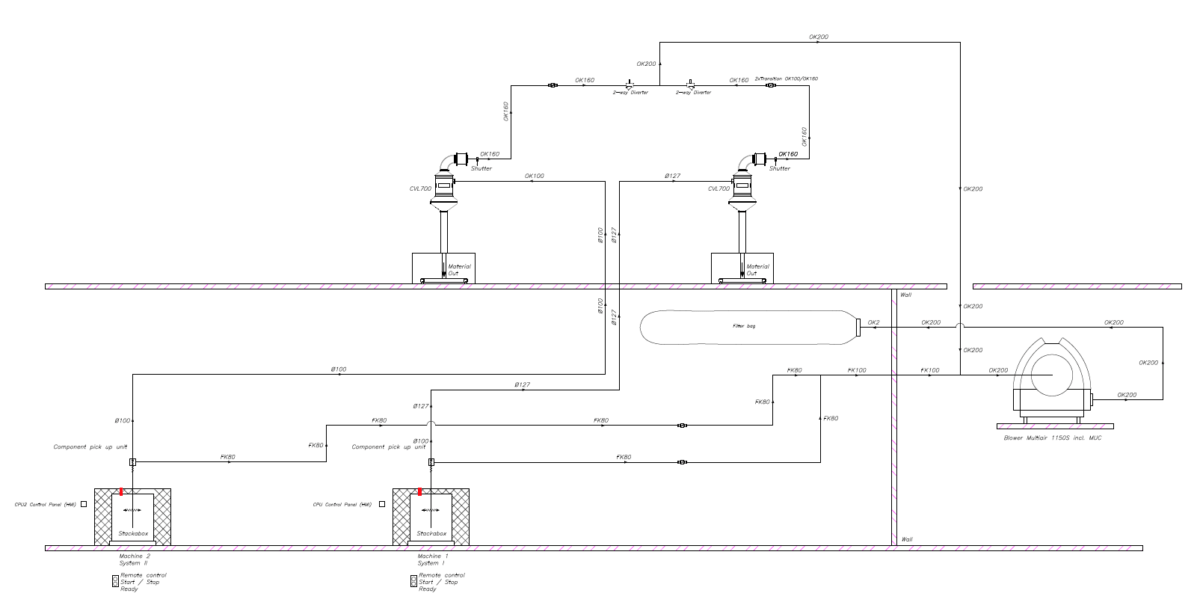
Les avantages et les bénéfices
- La combinaison sans faille de l’unité de ramassage et du chargeur de composants rationalise le transfert des composants en plastique de l’entrepôt aux lignes de production de bouchons.
- Le transport pneumatique et la livraison par lots à grande échelle de composants sont rapides et efficaces.
- Les processus qui étaient auparavant manuels sont désormais automatisés.
- Le système de transport est flexible puisqu’il fonctionne aussi bien à l’horizontale qu’à la verticale, laisse une faible empreinte et ménage les composants en plastique.
- Cette solution accroît la sécurité car le chariot élévateur ne fait plus de va-et-vient le long des lignes de production.
- Le travail est désormais plus ergonomique pour l’opérateur.
Les faits
- Matériau : Bouchons de bouteilles
- Dimensions, diamètre : Jusqu’à 80 mm
- Capuchon de poids du matériau : Jusqu’à 8 g/m2
- Quantité : +10 000 bouchons par heure et par ligne
- Machines : Deux machines à capsuler